Exploring the Technical Differentiation of Gaskets: Sealing the Path to Efficiency
In the world of engineering and manufacturing, where precision and reliability reign supreme, even the tiniest components play a pivotal role in ensuring seamless operations. One such unassuming yet critical component is the gasket. Often overlooked, gaskets are the unsung heroes that create a tight seal between two surfaces, preventing leaks, minimizing friction, and maintaining the integrity of mechanical systems. But not all gaskets are created equal. In this blog, we delve into the technical differentiation of gaskets, uncovering the diverse materials, designs, and applications that make these unassuming seals true engineering marvels.
1. Gasket Basics: A Seal of Approval
Gaskets are mechanical seals designed to fill the gap between two surfaces, ensuring a tight fit that prevents the escape of liquids or gases. They are used in a wide range of applications, from automotive engines and pipelines to aerospace systems and industrial machinery. The primary goal of a gasket is to create a reliable barrier that can withstand pressure, temperature fluctuations, and chemical exposure.
2. Material Matters: The Building Blocks of Gaskets
The choice of gasket material is perhaps the most crucial aspect of technical differentiation. Different materials offer varying levels of resistance to temperature, pressure, chemicals, and mechanical stress. Some common gasket materials include:
Rubber: Natural rubber, synthetic rubbers like neoprene, nitrile, and silicone rubber are popular choices for gaskets due to their flexibility and resistance to water and gases. They find applications in automotive engines, plumbing systems, and more.
Fiber: Materials like compressed non-asbestos fiber and cellulose are widely used for their compatibility with oils, fuels, and steam. These gaskets are often employed in pipelines and industrial equipment.
Metal: Metal gaskets, such as spiral wound gaskets and metal jacketed gaskets, are preferred when high temperatures and pressures are expected. They are used in applications involving steam, gases, and corrosive fluids.
Graphite: Known for its excellent chemical resistance and thermal conductivity, graphite gaskets are used in high-temperature applications, including those in the petrochemical and refining industries.
PTFE (Polytetrafluoroethylene): Also known as Teflon, PTFE gaskets excel in applications where chemical resistance is paramount. They are often used in pharmaceutical, food processing, and chemical manufacturing.
3. Shapes and Sizes: Gaskets Take Form
Gaskets come in various shapes and designs to suit specific applications:
Sheet Gaskets: These are flat, sheet-like gaskets cut into the desired shape. They are versatile and can be easily customized to fit different flange configurations.
Ring Gaskets: Typically made of metal, these gaskets are shaped like rings and fit inside flange grooves. They are used in applications requiring higher pressures and temperatures.
Spiral Wound Gaskets: Consisting of a combination of metal windings and a filler material, these gaskets offer excellent resilience and adaptability to fluctuating conditions.
4. Precision Engineering: Customization and Standards
Gaskets are often designed to meet specific industry standards and regulations. As engineering demands grow more intricate, custom gasket solutions are becoming increasingly common. Manufacturers employ advanced techniques like laser cutting and CNC machining to create gaskets tailored to unique system requirements.
5. Environmental and Economic Impact
"Like the hidden heroes of precision, gaskets bridge the gap between efficiency and integrity, sealing the promise of seamless engineering."
The choice of gasket material can have significant environmental and economic implications. Selecting the right material for a given application can lead to reduced maintenance costs, extended equipment lifespan, and decreased emissions due to leakage.
In conclusion, the world of gaskets is far from mundane. These seemingly simple components play a pivotal role in maintaining the efficiency and reliability of diverse mechanical systems. The technical differentiation of gaskets, encompassing material selection, design considerations, and application-specific customization, ensures that these unassuming seals continue to seal the path to operational excellence in various industries. So, the next time you encounter a smoothly running system, remember that gaskets might be the silent guardians ensuring its seamless operation.
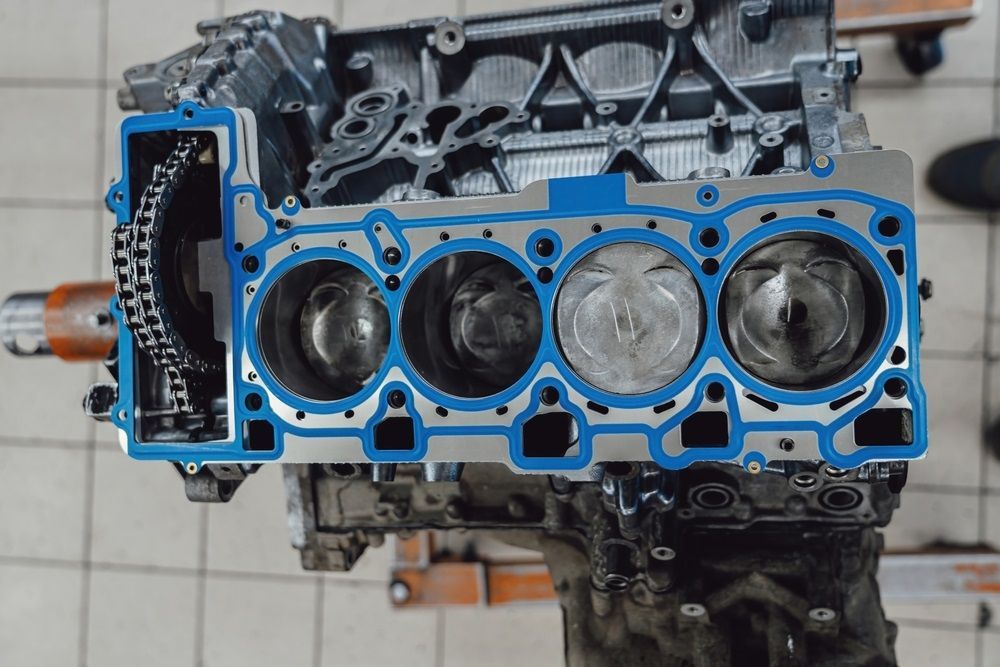