A Deep Dive into Gasket Manufacturing in India: Innovations and Growth
Introduction
Gaskets might seem like simple components, but they play a crucial role in maintaining the integrity of machinery and systems across various industries. In India, the gasket manufacturing sector has witnessed significant growth and innovation over the years. This blog explores the intricacies of gasket manufacturing in India, shedding light on its importance, manufacturing processes, key players, and the trends that are shaping the industry.
The Significance of Gaskets
Gaskets serve as seals between two or more surfaces, preventing leaks and ensuring that machinery and systems function smoothly. They are used in a wide range of applications, including automotive engines, industrial machinery, pipelines, refrigeration systems, and more. Gaskets are designed to withstand high temperatures, pressure, and chemical exposure, making them critical components in industries where safety and efficiency are paramount.
Manufacturing Processes
Gasket manufacturing involves several processes, each tailored to meet specific requirements:
Material Selection: Gaskets can be made from various materials such as rubber, metal, cork, and composite materials. The choice of material depends on factors like temperature, pressure, chemical resistance, and application.
Cutting and Shaping: Gaskets are usually custom-made to fit the contours of the surfaces they need to seal. Manufacturers use techniques like die-cutting, water jet cutting, and laser cutting to achieve precision.
Molding and Compression: For rubber and elastomeric gaskets, molding and compression processes are used. Rubber compounds are molded into the desired shape and then cured to achieve the required hardness and elasticity.
Metal Gaskets: Metal gaskets are often used in high-temperature and high-pressure applications. These gaskets are manufactured using techniques like stamping, laser cutting, and CNC machining.
Key Players in India
India boasts a vibrant gasket manufacturing industry with several key players dominating the market. Companies like Klinger, Champion Gaskets, Interface Performance Materials, and Spitmaan are well-known for their high-quality gasket solutions. These companies have not only embraced traditional manufacturing methods but have also incorporated advanced technologies to improve their products' performance and durability.
Trends and Innovations
The gasket manufacturing industry in India has witnessed notable trends and innovations:
Environmental Sustainability: With a growing emphasis on sustainability, manufacturers are increasingly developing eco-friendly gasket materials that reduce waste and environmental impact.
Advanced Materials: Innovations in material science have led to the development of gaskets that can withstand extreme conditions, ensuring reliability and longevity.
Digitalization and Automation: The integration of digital technologies and automation in manufacturing processes has improved efficiency, reduced errors, and accelerated production.
Customization: Industries are demanding gaskets tailored to their specific needs. Manufacturers are responding by offering customizable gasket solutions to meet unique requirements.
Quality Standards: Adherence to international quality standards is becoming a competitive advantage. Manufacturers are obtaining certifications to demonstrate their commitment to quality and safety.
Global Export: Indian gasket manufacturers are expanding their reach beyond domestic markets, exporting their products to various countries. This growth is attributed to competitive pricing and improved product quality.
Conclusion
The gasket manufacturing industry in India has come a long way, evolving from traditional methods to incorporating modern technologies and materials. Gaskets might be small components, but their impact on machinery and systems' performance is undeniable. As industries continue to demand higher standards of safety and efficiency, the gasket manufacturing sector will likely keep growing and innovating to meet these demands. With a focus on sustainability, quality, and customization, Indian gasket manufacturers are poised to play a significant role in shaping the future of various industries worldwide.
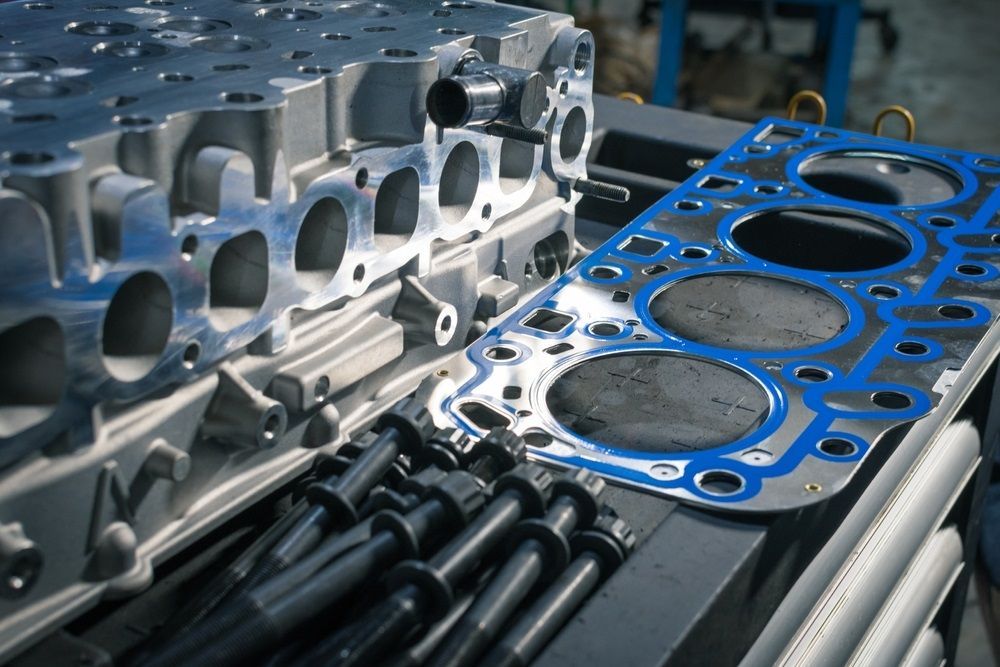
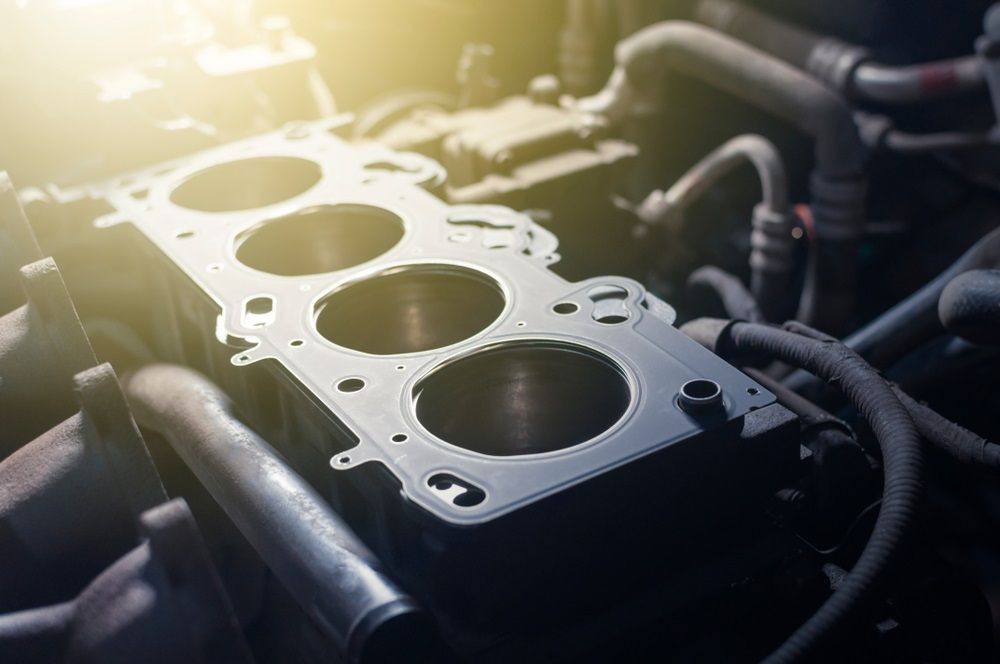